ジャストインタイム(Just-In-Time)とは
ジャストインタイム(JIT)は、必要な部品を、必要なときに、必要な量だけ製造・調達することを目的とした生産管理手法です。1970年代にトヨタ自動車が導入した「トヨタ生産方式(TPS)」に起源を持ち、在庫削減や生産効率向上を目的として、多くの製造業で採用されています。
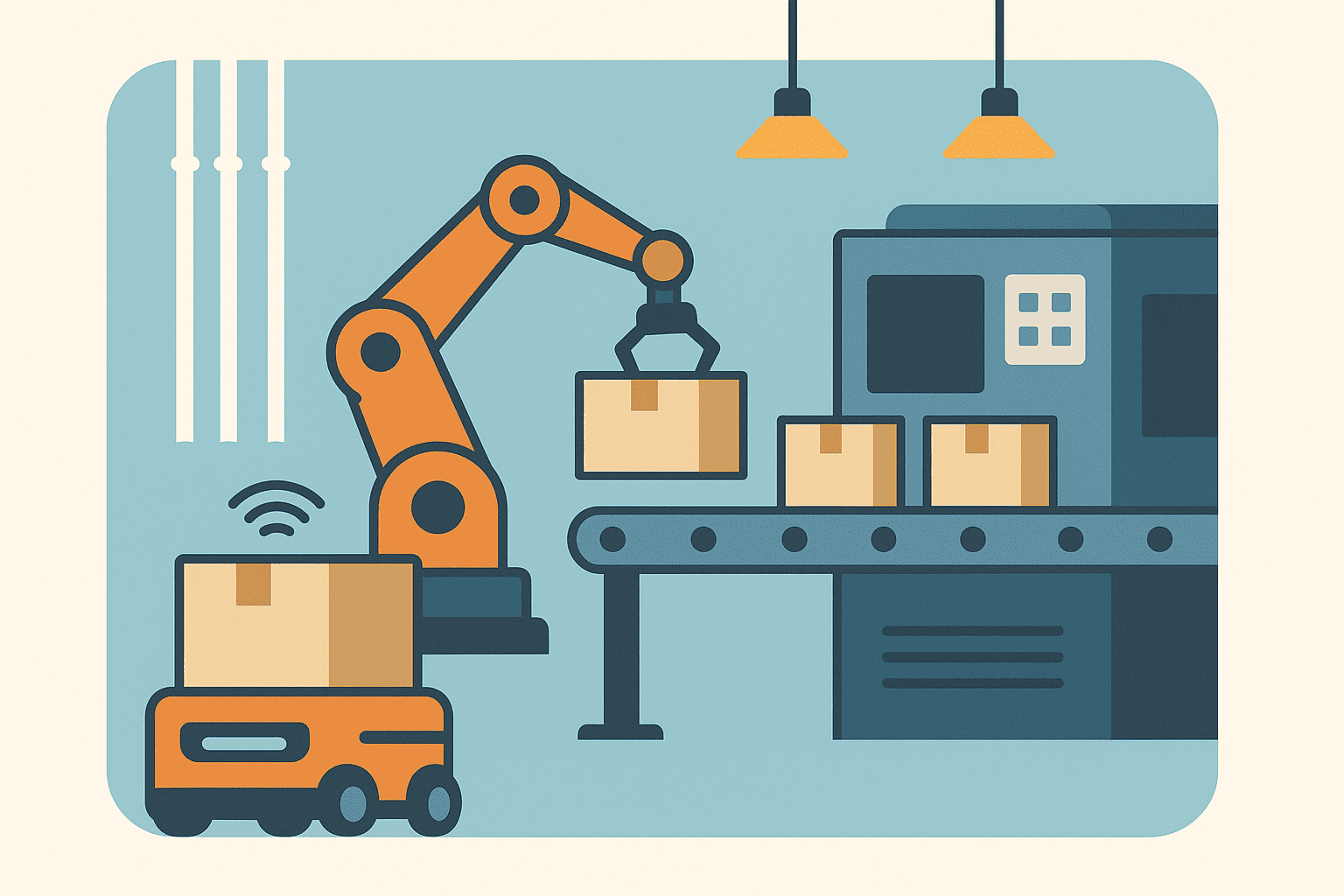
ジャストインタイムの起源と世界的な展開
JITは、1970年代にトヨタ自動車が抱えていた在庫コストの増加と資源の無駄という課題から生まれました。TPSの柱の一つとして体系化され、その後、アメリカやヨーロッパの製造業にも波及。現在では、自動車業界に限らず、電子機器、食品、アパレル、医療機器分野など幅広い業界で活用されています。
ジャストインタイムの基本原則
- 必要なものを、必要なときに、必要な量だけ生産する
- 在庫を最小限に抑えることで保管・管理コストを削減
- ムダの排除とカイゼンによる継続的な改善
- 供給業者・社内工程間の信頼関係と同期化が前提
ジャストインタイムとリーン生産方式の違い
JITとリーン生産方式はしばしば同義とされますが、厳密には異なります。JITは在庫の最小化を中心に据えた「供給タイミング」にフォーカスした考え方であるのに対し、リーン生産は「全体のムダ排除と価値最大化」を目指す包括的アプローチです。リーンでは6シグマ、TQMなど他の品質改善手法との併用が一般的です。
導入プロセスと実施ポイント
- 需要予測の精度向上:過去の販売データや市場動向を分析し、正確な生産計画を立案。
- サプライヤーとの連携:納期遵守率95%以上、納品リードタイム3日以内などのKPIを設定。
- 在庫可視化システムの導入:IoT・RFIDなどによるリアルタイム在庫把握。
- 社内教育と意識改革:JITの目的・意義を全従業員が理解し、改善提案制度などを推進。
プル方式とその効果
ジャストインタイムでは、「プル方式(Pull System)」が核となります。これは、後工程の要求によって前工程が生産を行う方式で、在庫滞留を防ぎ、フローの最適化を実現します。対義語は「プッシュ方式(Push System)」で、計画主導型の生産方法です。
項目 | プル方式 | プッシュ方式 |
---|---|---|
生産トリガー | 需要に応じて生産 | 計画ベースで生産 |
在庫量 | 最小限 | 過剰の傾向 |
柔軟性 | 高い | 低い |
品質管理との連携
JITの前提には「品質の安定」があります。なぜなら、生産後のチェックでは間に合わないため、リアルタイムの品質管理が求められるからです。「ゼロ・ディフェクト(欠陥ゼロ)」を掲げ、ポカヨケ、セル生産、全員参加型のQC活動が不可欠です。
ジャストインタイム導入のメリット
- 在庫コスト削減:倉庫スペースや保管費用を最大50%削減可能
- 生産リードタイムの短縮:リードタイムを30%以上短縮した事例も
- キャッシュフローの改善:不要在庫が減り、資金繰りが安定
- 品質向上:欠陥率の大幅な低減
ジャストインタイムの課題とリスク
- 災害・サプライチェーン寸断リスク:特に2020年以降、部品供給の遅延が大きな課題に
- 需要変動への脆弱性:急なオーダー増減に即応できない可能性
- サプライヤー依存度の高さ:一社集中によるボトルネックの発生
成功事例:実際の企業によるジャストインタイム活用
- トヨタ自動車:JITの発祥企業として、1980年代から現在に至るまで継続的に改善と成果を重ねている。
- デル(Dell):注文後に組み立てを行う「ビルド・トゥ・オーダー」方式で在庫レス経営を実現。
- ハーレーダビッドソン:JIT導入により部品在庫量を25%以上削減、生産リードタイムも短縮。
- ホンダ:JITに加え、日米間のグローバル物流最適化も行い、安定供給体制を構築。
まとめ
ジャストインタイムは、単なる在庫削減手法ではなく、製造業の競争力を高める包括的な戦略です。成功には、精密な計画、強固なサプライチェーン、現場の改善文化が不可欠です。リスクを適切に管理しながら、JITを正しく運用することで、持続可能で柔軟性のある生産体制の構築が可能となります。